標準原価計算 Standard Costing
標準原価と原価標準
標準原価計算システムの下では、標準原価または予定原価が製品原価として割りてられることになる。原価標準(cost standard)は、製品1単位を製造するのに必要な経済的要素の投入量・消費量(input)と標準原価の積で表される。
ここでは、直接材料費だけを例にとる(材料費だけで製品を造れるという理解のための仮定)。
製品1単位を生産するのに、標準で5kgの鉄材がげ必要だとする。鉄材1kg当たりの材料費が標準で@3円/kgだとする。
- 製品1単位を生産するために、鉄材が5kgだけ標準消費量として必要になる
- 製品1単位を生産するために、鉄材1kgあたり標準価格として@3円/Kgだけ必要である
※筆者は文章にした際の可読性を上げるために、敢えて、”単価”の意味を表す”@”と、”/kg”とか”/h”を併記する癖(工夫)をつけている。確かに「馬から落馬」の類の重言だが、意外にこれが便利なのである。
原価標準(cost standard)とは、製品1単位を製造するのに必要な標準原価を意味するから、
- 原価標準 = 標準消費量 × 標準価格 = 5kg × @3円/kg = @15円/個
となる。
ここで、実際の製品の生産量が25個だとしたら、25個の完成品の標準原価は、
- 標準原価 = 原価標準 × 生産量 = @15円/個 × 25個 = 375円
となる。
原価標準カード
前章のように、直接材料費のみで原価計算が完結することは実務的には考えにくい。よくある一般的姿は、直接材料費、直接労務費、(直接経費、)製造間接費の3つ(ないしは4つ)に原価要素を分けて原価計算を実施する。
このような形態別×直間別の原価分類に従って標準原価制度を整備するとしたら、
原価要素 | 標準消費量 | 標準価格 | 原価標準 |
---|---|---|---|
直接材料費 | 標準使用量 5kg/個 | 標準消費価格 3円/kg | 15円/個 |
直接労務費 | 標準作業時間 2時間/個 | 標準賃率 4円/時間 | 8円/個 |
製造間接費 | 標準配賦基準 2時間/個 | 標準配賦率 5円/時間 | 10円/個 |
合計 | 33円/個 |
となる。
このような原価標準を作成するのに必要なデータを一覧化したもの、またはそうしたデータに集計結果である原価標準カードを含めて、「コストテーブル」と呼称することが多い。
初学者が最初に陥る難所 - allowed for the actual input
ただ単純に、標準消費量×標準価格で標準原価(厳密には原価標準だが)を求めればよいのに、多くの初学者が資格試験における標準原価計算の問題を間違えたり、実務者でも標準原価計算システムの設計や運用で設定を間違えたりする。
ふたたび、簡略化のため、直接材料費(鉄材)のみで製品を造る例を用いる。
- 原価標準 = 標準消費量 × 標準価格 = 5kg × @3円/kg = @15円/個
素直に、この@15円/個に生産量を掛けることで標準原価が楽に求まる。
- 標準原価 = 原価標準 × 生産量 = @15円/個 × 25個 = 375円
しかし、試験問題や実務での管理計数では、実際消費量:150kg(6kg×25個)という情報が与えらえて、初学者や実務初心者を惑わす罠となってしまう。
典型的な間違い(その1)知らない間に実際消費量を用いてしまうケース
仕損・減損に関する情報が提示されていない場合に限り、消費量(input)は全て生産高(output)に転化されたとみてほぼ間違いない。
この常識に囚われ過ぎて、原価標準を用いて標準原価を計算すべきところ、自分で勝手に、実際消費量と標準価格を掛け算して、自己流標準原価を創り出してしまうことがある。
【間違い】標準直接材料費 = 実際消費量 × 標準価格 = 150kg × @3円/kg = 450円
標準原価計算において実際値を用いるのは、生産高(製品の数)であって、消費量ではない。
ここで、実際消費量を用いてえせ標準原価を計算してしまったら、数量差異分析ができなくなってしなう。
実際消費量と標準消費量の違いは、「数量差異」として、標準原価計算における重要な管理項目のひとつになっているのだ。
敢えて同じ手順を踏んで標準原価(直接材料費)を求めてみるなら、
【正しい】標準消費数量 = 実際生産高 × 標準使用量 = 25個 × 5kg/個 = 125kg
【正しい】標準原価 = 標準消費数量 × 標準価格 = 125kg × @3円/kg = 375円
※詳解は別稿に譲るか、上例では、消費量差異(数量差異)が 375円-450円=▲75円(不利差異)になる
典型的な間違い(その2)勝手に生産高を決めつけてしまうケース
「実際消費量:150kg(6kg×25個)」という記述で情報提示がなされれば、まだ誤解が生じる余地を減らすこともできようが、これが「実際消費量:150kg」とだけある場合、さらに曲解する者が現れてしまう可能性を高める。
【間違い】実際消費量 ÷ 標準使用量 = 実際生産高
【間違い】150kg ÷ 5kg/個 = 30個
【間違い】標準直接材料費 = 実際生産高 × 原価標準 = 30個 × @15円/個 = 450円
こちらは、正しく原価標準を使用しているにもかからず間違ってしまう例である。
アカデミックな学者様が記述する教科書には正論しか書かれていない。あまり、実際の間違い例まで開設したものはない。
逆にWebで目にする解説記事は、「標準原価」と「原価標準」の使い分けすらされていないものも目立つ。
使える原価管理を身に着けるためには、アンチパターンにも気を配っておきたいものだ。
製造間接費の配賦
標準原価計算システムにおける製造間接費の配賦基準はあらかじめ設定されている(predetermined)ことがほとんどだ。
伝統的な配賦計算の場合、以下のように配賦レートを求めることができる。
\( \displaystyle \bf 配賦レート=\frac{製造間接費発生額の予算額}{配賦基準となる予算操業度} \)
標準原価の設定レベルの厳しさの調整次第のところがあるが、概ね、原価標準の設定目的は目標管理であるところから、これを予算制度と連携させ、標準原価≒標準原価として運用した方が色々と都合がよい。
配賦基準として最も適切なコストドライバーを割り当てることが肝要となる。それは、製造間接費が一体どのように発生して、製品の製造活動にどのように関連しているかで見定めることになる。
例えば、労働集約的な製造工程であるならば、直接作業時間や機械時間が適切な配賦基準となる可能性が高い。
製造間接費の原価標準 = 配賦レート × 配賦基準
製造間接費の原価標準 = @5円/時 × 2時間/個 = 10円/個
このとき、生産数量が25個だとしたら、
製造間接費の標準原価 = 原価標準 × 実際生産数量 = 10円/個 × 25個 = 250円
となる。
原価差異について
製造間接費について、標準原価を事前に設定済みの原価標準(配賦レート)で計算すると、これもやはり実際原価との間で差額が生じることになる。
もちろん、これも原価差異として処理するのだが、配賦レートと配賦基準の双方が共に事前の標準設定値を用いるものであるから、いわゆる単価(レート)差異と数量差異の双方が生じる可能性がある。
製造間接費の場合、会計実務的には、圧倒的に数量差異の変動が大きいため、特に注目度が高くなる。
標準数量より実際の生産数量が上回ったときは、配賦超過(over-applied cost)、下回ったときは、配賦不足(under-applied cost)となる。
これは、標準原価計算システムにおいて、配賦レートが標準で事前に決定されているため、生産実態に応じて、標準より多くを生産してしまったら、配賦額もその分、標準で考えたより多い金額が配賦される。
逆に、標準より少ない生産数に留まったら、実際に発生してしまった製造間接費より少ない金額しか配賦されなくなる。
これでは、期間損益計算に正確性という難点が残ってしまう。そこで、実際原価と標準原価の差額(原価差異)に関する会計処理が各国のGAAPで定められている。
概論でこれをまとめると、
- 差異が僅少である場合、差異の100%を当期の製造原価(売上原価)に含める
- 差異が多額になった場合、当期の生産数量に割り当てられた金額を、当期の製造原価(売上原価)と関連する棚卸資産に比例按分する
仮に、標準原価差異を全て製造原価(売上原価)に割り当てるとしたら、期末棚卸資産の評価額は標準原価そのものになる。
標準原価システムは、経営者に対して、実際の生産数量の範囲内において、実際発生額と目標とすべき標準原価の差異を明らかにして報告してくれるという業績管理・予算管理プロセス上のメリットを与えてくれる。
原価管理・予算管理プロセスとの関係
全部原価計算における標準原価差異に関するレポートは、決算期を待って、全ての支出のインボイスが集計され、期間費用(期間原価)が計算された後に情報を提供してくれる。
よって、レポートが遅れれば遅れるほど、現場管理への変更指示が遅れてしまうことになる。
作り過ぎによる在庫調整や、市場需要の急変対応のための製造品種の変動(段取り替え)、購入品目とサプライヤーの切り替え、直接工のシフトなど。
一方で、変動原価計算に基づく変動予算制度において、標準原価が用いられれば、製品の生産または出荷(売上)時点で(まあ実務的には電算処理にかかるタイムラグは必須だが)速攻で採算(原価)が分かるようになる。
このように、標準原価システムは、変動予算制度と相まって、レポートの迅速化、ひいてはPDCAサイクルの短期化に役立つ経営管理ツールのひとつである。
標準原価計算システムは、実に幅広い業種・業態で活用されている。
製造業の場合は、変動予算制度と組み合わせて、直接材料費と直接労務費のコントロールに役立てる。
サービス業、例えば、ファーストフードチェーンなどでは、標準原価システムの採用率が高い。なぜなら、労働集約的な職場を多く有する彼らにとって最大のコストは人件費(直接労務費)だからだ。
世界で発売・運用されているメジャーどころのERP(Enterprise Resource Plannning、企業資源計画、統合基幹業務システム、基幹システム)は、標準原価システムを標準装備している。
発売元(開発元)は、リアルタイムと言っているけれど(やはり電算処理のタイムラグやインボイスの集計のためのタイムラグは実務上発生が不可避なのだが)、まあほぼ生産完了オーダーが上がった時点での損益(採算)が分かるようにはなっている。
基幹システムの再構築プロジェクトを遂行する際、標準原価計算システムを改めて導入する企業もまだまだ多く存在するのも事実である。
【参考】標準原価・正常原価・実際原価
原価測定方法 | 原価集計方法 との組み合わせ | 直接原価の 賦課レート | 直接原価の 賦課基準 | 間接原価の 配賦レート | 間接原価の 配賦基準 |
---|---|---|---|---|---|
標準原価 | ・総合原価計算 ・個別原価計算 | 標準レート | 標準消費量 × 実際生産高 | 事前測定 による 標準レート | 標準基準値 × 実際生産高 |
正常原価 | ・個別原価計算 | 実際レート | 実際消費量 × 実際生産高 | 事前見積もり による 正常レート | 実際基準値 × 実際生産高 |
実際原価 | ・個別原価計算 | 実際レート | 実際消費量 × 実際生産高 | 実際レート | 実際基準値 × 実際生産高 |
原価管理 Cost Management 体系
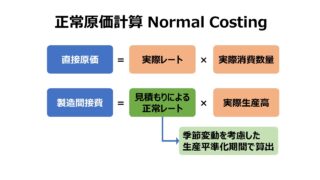
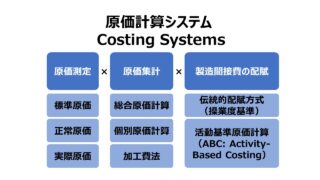
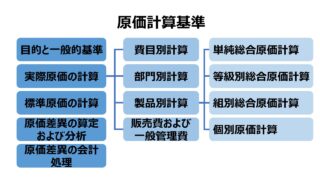
コメント